The Expert's Guide to Effective Casting Aluminum Illinois
The Expert's Guide to Effective Casting Aluminum Illinois
Blog Article
Technology in Light Weight Aluminum Spreading: Cutting-Edge Techniques for Modern Makers
What absolutely establishes these innovations apart are the lasting aluminum alloys being created and the high-pressure die casting methods that are transforming the sector. Join us as we explore the forefront of light weight aluminum spreading innovation, where modern technology fulfills creative thinking to redefine what is feasible in the globe of metal spreading.
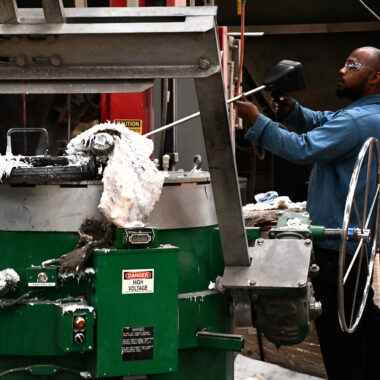
Advanced 3D Printing Methods
Utilizing cutting-edge additive production procedures, progressed 3D printing strategies have transformed the manufacturing of elaborate and personalized aluminum parts. By utilizing high-precision printers that can collaborate with aluminum powders or filaments, manufacturers can create intricate geometries and layouts that were formerly unattainable via traditional manufacturing techniques.
One of the essential benefits of advanced 3D printing in light weight aluminum component production is the capability to achieve light-weight yet durable frameworks. This is especially advantageous in sectors such as aerospace and automobile, where weight decrease is vital for improving fuel effectiveness and overall efficiency. Additionally, the customization alternatives used by 3D printing enable the manufacturing of special and customized parts that satisfy certain demands, leading to improved capability and performance.
Moreover, the effectiveness of the 3D printing procedure decreases material waste and reduces the general production time, making it a cost-effective option for making light weight aluminum components. As innovation remains to advancement, the abilities of 3D printing in light weight aluminum manufacturing are expected to expand, using also better possibilities for development in various sectors.
Computer-Aided Style Advancements
With the improvements in innovative 3D printing techniques for aluminum parts, the assimilation of Computer-Aided Layout (CAD) software program has actually become increasingly crucial in driving advancement and effectiveness in the manufacturing procedure. CAD developments have actually changed the means designers and designers develop aluminum spreading molds by offering exact digital modeling abilities. These software program devices permit the development of intricate styles and simulations that optimize the spreading process, resulting in better elements.
Among the key benefits of CAD in aluminum casting is the ability to identify potential issues early in the layout stage, reducing costly mistakes and revamp during manufacturing. By mimicing the casting process practically, designers can assess variables such as cooling down prices, material circulation, and structural integrity prior to a physical mold is developed. This proactive strategy not just saves time and sources however likewise makes sure that the final aluminum elements satisfy the preferred specifications.
Moreover, CAD software program makes it possible for fast versions and modifications to designs, promoting quick prototyping and modification to satisfy details needs. By leveraging CAD innovations in light weight aluminum casting, manufacturers can streamline their processes, improve product quality, and remain at the forefront of advancement in the sector.
High-Pressure Die Casting Techniques
High-pressure die spreading techniques are commonly recognized for their efficiency and precision in producing complex light weight aluminum components. By using high stress to compel molten aluminum into elaborate mold and mildews at rapid speeds, this technique allows for the production of thorough and dimensionally precise components. One of the key benefits of high-pressure die spreading is its ability to generate parts with thin wall surfaces and fine information, making it excellent for applications where light-weight yet strong parts are essential.
The process starts with the preparation of the die, which is typically made from solidified tool steel and consists of 2 halves that create the desired part shape. The liquified light weight aluminum is then injected into the die cavity under high stress, guaranteeing that the product loads all the elaborate attributes of the mold. When the light weight aluminum strengthens, the die opens up, disclosing the completed part prepared for any kind of needed post-processing.
High-pressure die spreading is commonly utilized in various industries, including automobile, aerospace, and electronic devices, where high-volume manufacturing of complicated aluminum parts is needed. casting aluminum illinois. Its capability to supply limited resistances, exceptional surface finishes, and cost-effective production makes it a favored option for modern-day designers aiming to innovate in light weight aluminum spreading strategies
Lasting Aluminum Alloys Growth
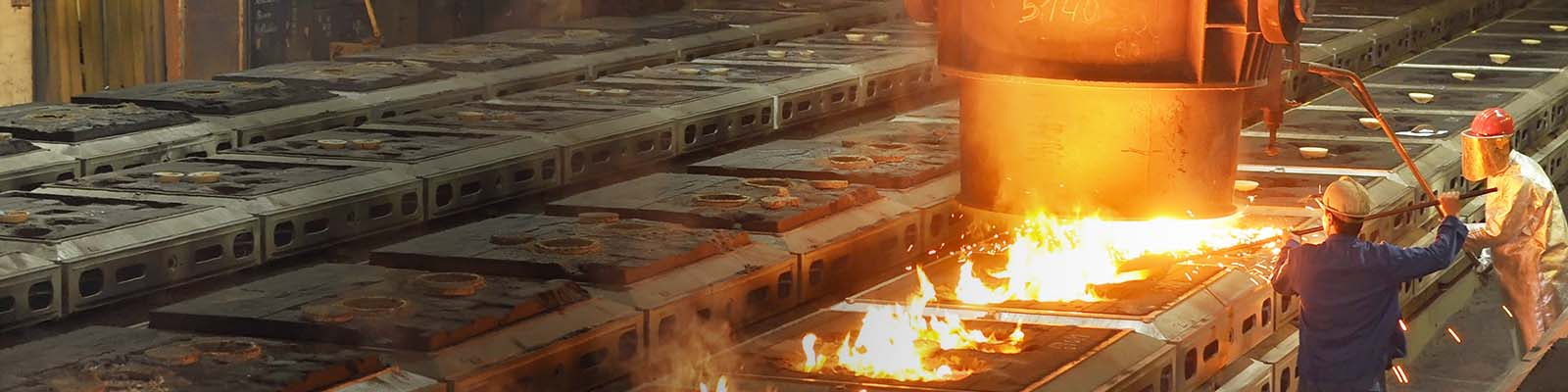
One method to lasting light weight aluminum alloy growth entails incorporating recycled aluminum material right into the alloy structure. By making use of go to this website recycled aluminum, manufacturers can lower power intake and greenhouse gas discharges associated with main aluminum manufacturing. Furthermore, recycling light weight aluminum helps divert waste from land fills, adding to a much more round economic situation.
Moreover, researchers are checking out new alloying aspects and handling techniques to improve the sustainability of light weight aluminum alloys. By maximizing alloy compositions and producing processes, it is possible to boost the recyclability, sturdiness, and general ecological performance of aluminum items.

Automation and Robotics Integration
In the world of sustainable light weight aluminum alloys advancement, the combination of automation and robotics is changing manufacturing procedures, leading the way for enhanced performance and precision in manufacturing. Automation and robotics are improving conventional casting strategies, using countless advantages to creators in the light weight aluminum industry. By incorporating automation right into the casting process, recurring jobs that were once labor-intensive can now be successfully taken care of by robotic systems, minimizing the danger of human error and boosting overall performance.
Automated systems can work around the clock, making sure a website link continuous production cycle that reduces downtime and maximizes outcome. Robotics integration enables complex mold and mildews and complex styles to be generated with unparalleled precision, fulfilling the demands of contemporary creators for high-grade light weight aluminum components. In addition, using automation in casting operations promotes a safer working setting by minimizing the exposure of employees to unsafe problems.
Verdict
To conclude, the developments in aluminum casting have actually transformed the manufacturing market. Advanced 3D printing techniques, computer-aided layout developments, high-pressure die spreading approaches, lasting light weight aluminum alloys development, and automation and robotics assimilation have all added to the innovation of the spreading procedure. These cutting-edge techniques have actually allowed designers to produce complex and high-quality light weight aluminum products efficiently and successfully. The future of light weight aluminum casting is bright with continuous technology and technological innovations.
What absolutely sets these advancements apart are the sustainable light weight aluminum alloys being developed and the high-pressure die spreading techniques this that are changing the sector. Join us as we discover the leading edge of light weight aluminum casting advancement, where modern technology satisfies imagination to redefine what is possible in the world of steel casting.
One approach to lasting aluminum alloy advancement entails integrating recycled light weight aluminum content into the alloy composition - casting aluminum illinois. By utilizing recycled aluminum, manufacturers can lower power usage and greenhouse gas exhausts associated with key light weight aluminum manufacturing. Advanced 3D printing techniques, computer-aided design technologies, high-pressure die casting techniques, lasting aluminum alloys advancement, and automation and robotics combination have all contributed to the innovation of the casting process
Report this page